What Is the Future of PLM Tools in the Era of Industry 4.0?
"Change is hard because people overestimate the value of what they have and underestimate the value of what they may gain by giving that up." - James Belasco and Ralph Stayer.
Industries are always looking for ways to minimize costs, shorten the time to market, and ensure top-notch quality. A study by McKinsey & Co. reveals that a delay of six months can result in 33% less profit. Effective product lifecycle management software can help reduce the time to market and achieve other objectives.
The product lifecycle management software market is expected to grow to 22.57 billion dollars by 2025, which reveals the crucial nature of software tools in the industrial sector. PLM tools are designed to increase productivity, reduce costs and compliance risks, enhance innovation, and help get a product to the market faster. What are PLM tools?
Before learning about best PLM tools, it is important to understand Industry 4.0 and its impact on the manufacturing sector. Industry 4.0 denotes smart manufacturing, wherein the following achievements have made the industrial sector effortlessly efficient.
It symbolizes complete digital transformation, enabling improved productivity, agility, flexibility, and decision-making. Some of the technologies that Industry 4.0 uses include AI, machine learning, cloud computing, the Internet of Things, and more.
The industry's market size was USD 135.38 billion in 2023 and is expected to reach USD 884.84 billion by 2034. Automation and the use of smart machines form the core of Industry 4.0. They enable manufacturers to increase their productivity and efficiency. Increased information transparency helps in better decision-making.
So, back to the question of what PLM tools are. They are software applications that enable organizations to create new products in an efficient, sustainable, and collaborative way. PLM tools are undergoing a significant transformation to adapt to the demands of Industry 4.0, focusing on data-driven decision-making, digital twins, and advanced analytics. Here is more on PLM tools and their impact on industries.
Understanding the Convergence of PLM and Industry 4.0
With the advent of Industry 4.0, manufacturing businesses have radically changed. Unlike the conventional methods that rely on manual input, Industry 4.0 has many advantages. It uses core principles such as:
- Information transparency and virtualization
- Interoperability and interconnection
- Real-time capability
- Decentralization and autonomous decision-making
- Modularity
- Technical assistance and service orientation.
Automation is a key principle that has led to the smart factory concept. This involves a flexible but well-connected system that processes data to enhance itself and adapt to new challenges. Applying the principles involved integrates information and processes it in real-time, achieving an efficient and fully agile system. Productivity is increased due to reduced downtime in production and the ability to adapt to new demands in product alterations.
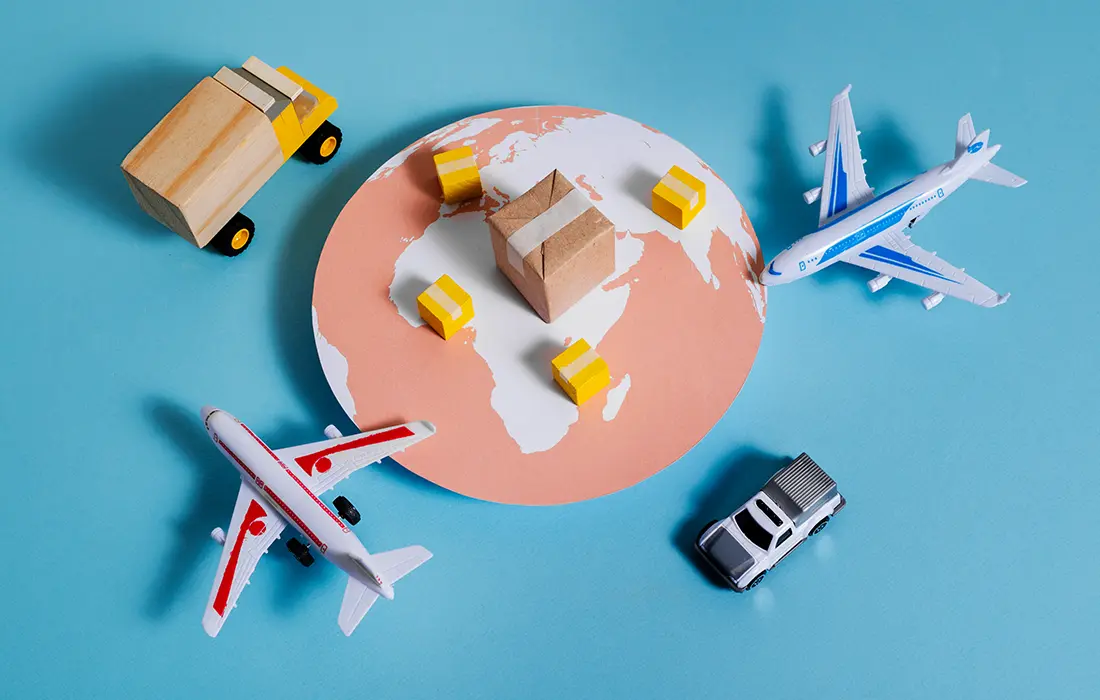
Opportunities that arise from the convergence of Industry 4.0 and PLM
A key advantage of integrating PLM and Industry 4.0 is the enhanced user experience. Interactive technologies help to meet customer expectations of usable, efficient, and effective products. With more advanced technologies taking over the manufacturing and design elements, it is necessary to combine the various components involved, such as:
- Electronic
- Mechanical
- Software
The use of connected devices and other Industry 4.0 technologies makes reducing or eliminating the gaps between the design and its real-world application possible. While earlier, implementing such technologies was exclusive to the design field, now, with the Industry 4.0 convergence, it can produce efficiency and performance. Some of the areas that have benefited include:
- Digitalization enables the evaluation of digital data and the extraction of business and customer value.
- With PLM covering the entire product cycle, its integration helps combine processes, people, information, and business systems. They can be viewed from a single window for better analysis.
- Digital manufacturing, data mining, predictive analytics, data migration, simulation, digital manufacturing, and optimization are more enhanced.
- IoT has transformed how product design, development, manufacturing, and support are organized and executed.
With cloud adoption, companies expect higher returns via better performance, security, and scalability. It also enables improved enterprise collaboration with purpose-built and role-based applications. The cloud-based PLM market is expected to reach USD 55.55 billion in 2024 and USD 190.82 billion by 2031.
Challenges faced by industries
Connecting PLM tools and IoT is not about feeding company information to PLM systems. It involved managing the lifecycle of the data, analyzing the multiple data points, and, in short, deciphering unstructured data. Since PLM involves structured data analysis, machine learning, data analysis, and other Industry 4.0 tools can be a game changer. Some of the challenges that businesses can face include:
- A reduced product lifecycle and the need to outsource many components to different firms result in a complicated product structure.
- The virtual design of products is necessary for diverse supply chain aspects and design teams to collaborate.
- There is a need to use net-centric technology that will help make the present enlarged business model free of its inherent value.
- Managing projects, exchanging, and maintaining product information is a big challenge.
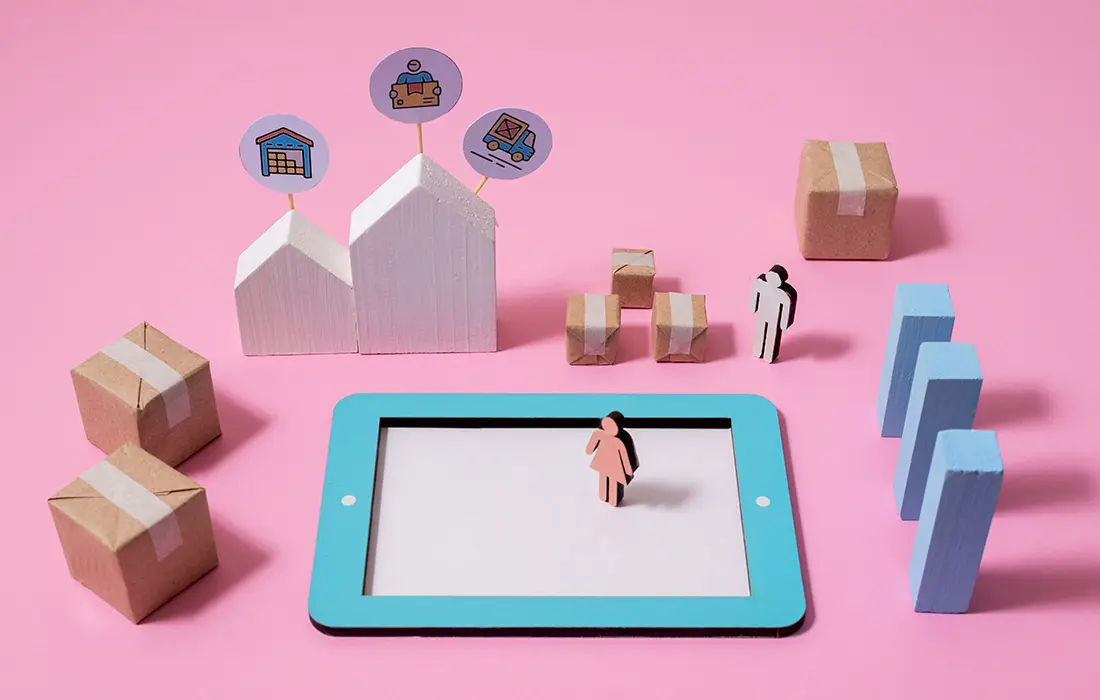
The importance of data integration and interoperability for successful implementation
Interoperability enables effective data sharing, while data integration helps maintain consistency and accuracy. Data quality is improved as disparities are minimized, and consistency is assured. An integrated product lifecycle management software solution helps streamline data, which results in secure information exchange. Encryption of sensitive information helps add an additional security layer.
Better team collaboration and quicker time to market are possible. With Industry 4.0 technologies like digital twins, a virtual environment is used to train algorithms and validate them in the development of autonomous vehicles. The use of VR and AR in PLM helps in virtual prototyping. By integrating diverse technologies with PLM, an organization can meet its needs comprehensively.
Further, the integration helps connect different enterprise systems, such as Enterprise resource planning, customer relationship management, etc., with Industry 4.0 technologies. This is vital to automating administrative, operational, and physical assets and streamlining supply chain collaboration.
Agile product lifecycle management software helps in effective collaboration, allowing easy exchange of information related to products and processes. It enables long-term retention and traceability of data. Due to the interlinking of different technologies, any constraints present in interoperability are removed.
Key Trends Shaping the Future of PLM
The highly competitive industrial sector makes it imperative for organizations to launch new and innovative products. Some of the key trends that shape the future of PLM are:
Data-Driven PLM
Data is a key part of business processes and a major influencing force in product development. A Gartner survey reveals that by 2025, 80% of companies looking to scale their digitalization efforts will fail because they will not adapt to modern data usage methods.
Companies need to efficiently evaluate data and integrate it into the various development stages. Big data and analytics help companies develop more customer-centric products, adding customer value and reducing risks linked to product launches. Big data can help in many ways.
1. Get actionable insights with the help of tools such as predictive analytics and data mining
They can know customer needs and the demand for a product, resulting in a proactive product development approach. This ensures better quality and consistency and reduces failure risk.
2. Improve existing products, such as using customer feedback to get insights
Companies can also use data from social media and other online avenues to understand customer needs. Using such data can help firms to provide solutions that keep up with the current trends.
3. Develop new products by using data for informed decision-making
Optimization models strengthen decision-making and improve performance to achieve more ROI. They also help predict quality limitations and ensure top-quality products.
Digital Twin Technology:
Digital twin technology involves creating virtual replicas of products and processes. These replicas are connected to product information as it passes through different phases. There are many types of digital twins, and all of them cover processes, data, and relationships by linking the various system stages.
Benefits of digital twins for product development and lifecycle management
Digital twins help monitor performance continuously. They help analyze data from sensors used in physical assets. The technology helps to:
- Identify specific patterns
- Optimize processes
- Improve overall performance.
The various benefits result in a cost-effective and efficient production environment. Manufacturers can make informed decisions, improve processes, and ensure seamless information flow throughout the product's lifecycle.
Another upside of the technology is that it can be used in conjunction with other Industry 4.0 technologies, like AI and IoT, to form a complete and precise product representation. This improves predictive maintenance and supply chain efficiency.
Integration of digital twins with agile PLM systems
By using digital twins in agile PLM systems, companies can achieve many important tasks, like
- Simulate and test the performance of a product
- Monitor the condition of the product
- Predict when repairs or maintenance will be needed.
Companies can improve their decision-making process and efficiently collaborate to reduce costs and time linked with physical testing. Although the technology is expensive and complex, its benefits make it a must-have for companies looking to grow and gain an edge over their competitors.
AI and Machine Learning in PLM
Adding Artificial Intelligence and Machine Learning technologies to agile product lifecycle management software has brought several benefits. Here are a few important advantages:
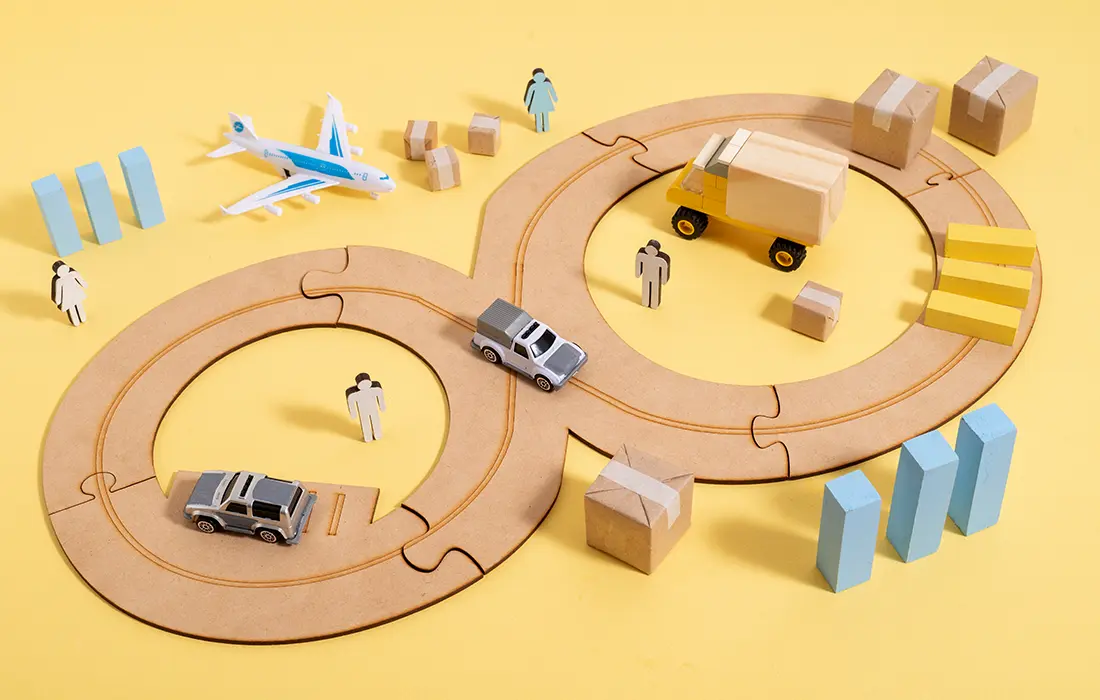
Automation of routine tasks
AI algorithms help automate routine tasks like document management, quality assurance, and more, freeing up valuable time and effort that can be channeled to other strategic initiatives. Automating tedious tasks helps speed up the design process and reduce overall time to market.
Design optimization and generative design
With the current focus on customer-centric product design, AI and ML-powered systems can help immensely. They can effectively meet consumer needs by providing insights into customer needs based on historical data and market trends. AI algorithms improve design processes by
- Generating innovative ideas
- Performing simulations
- Optimizing the design for manufacturability and performance
- Intelligent product lifecycle management
By seamlessly integrating artificial intelligence and machine learning technologies, efficiency, innovation, and agility across a product's lifecycle can be enhanced. Generative AI opens up exciting opportunities for the production, marketing, sales, and service sectors. In a Salesforce survey, 68% of people stated that the technology will help them better serve their customers.
The integration makes adapting to changing marketing dynamics, technological advancements, and customer needs easier. This fosters continuous and consistent innovation and improvement. With optimized processes and unrivaled insights, businesses can gain a competitive edge.
Cloud-Based PLM and Collaboration:
Using a cloud-based system can revolutionize the development process and optimize the management. It offers plenty of benefits to help businesses streamline and innovate their processes.
- Save infrastructure costs with a cloud setup where the cost is spread among the cloud server's clients, making way for cheaper costs. Serverless cloud computing can reduce infrastructure costs by nearly 70%.
- Faster implementation is possible with the simple and fast on-cloud PLM.
- Instant scalability without additional costs can be achieved by using subscription-based cloud PLM systems.
- Support and maintenance costs are lower when compared to in-house systems.
Enhanced collaboration and knowledge sharing
With collaborative agile product lifecycle management software, the various stakeholders in a product's lifecycle are better coordinated and collaborated. Cloud computing, social media, digital twins, and other such tools help in information exchange and other aspects of development.
Collaboration helps integrate processes and data across the supply chain. This enables knowledge sharing, resulting in quicker and more effective problem-solving, minimal errors, and improved quality.
Scalability and flexibility
A cloud-based system allows scalability, as it is easy to manage storage, processing, and other aspects of the PLM system based on demand. Flexibility is also possible, as the agile product lifecycle management software integrates with cloud-based tools and services like security, collaboration, and analytics.
Top PLM Tools and Their Capabilities
Industries rely heavily on product development software as it helps to plan and manage their work. New products reach the market quickly and have better quality and customer satisfaction. When industries know what PLM tools work effectively, they can ensure successful outcomes from their application. Here are some of the top agile PLM systems, which are explained in detail.
1. 3DEXPERIENCE by Dassault Systèmes
https://www.3ds.com/products/product-lifecycle-management
As a revolutionary tool for product development, 3DExperience provides virtual twin experiences that combine virtual and real worlds for effective development.
Key features and functionalities:
- Connects an organization's entire ecosystem using a single unified environment, providing secure and real-time collaboration.
- It helps design and visualize a virtual twin of operations, processes, and products, enabling a closed-loop virtual-real-world connection.
- Allows teams to imagine, design, and test innovative processes, materials, and products that nurture a sustainable economy.
- As a cloud-based platform, it allows businesses to get their products to market faster and with proven outcomes.
2. Siemens Teamcenter
https://plm.sw.siemens.com/en-US/teamcenter/
Teamcenter is recognized by Forrester Research as one of the leading agile PLM products in the market. Its innovative platform helps solve the toughest product development challenges.
Key features and functionalities
- It uses digital twin technology to connect processes and optimize them for designs, software, systems, simulation, and visualization.
- The tool helps automate product lifecycle processes, connect people across the lifecycle, and provide visibility to ensure innovative and successful outcomes.
- Provides a single information source for products to each stakeholder in a business.
- Streamlines lifecycle processes by managing and automating them, reducing change cycle time, and controlling costs.
- Its closed-loop change management helps to use flexible processes that can be customized to meet specific needs.
3. SAP PLM
https://www.sap.com/products/scm/plm-r-d-engineering.html
SAP's agile product lifecycle management software helps build a sustainable and risk-resilient supply chain. Its digital thread helps in faster decision-making.
Key features and functionalities
- Helps define, develop, and provide top-quality sustainable products via innovative development systems.
- Enables collaborative and faster product development by ensuring access to relevant insights and information.
- Uses digital twins to combine engineering models and data and create closed loops for product life cycle synchronization.
4. Aras Innovator
Aras is an agile PLM product that offers an open and adaptable solution. It has an extensive product data platform, a composable application framework, and low-code development that ensures an effective and faster time to market.
Key features and functionalities
- Reduces time-to-market delays and rework costs and lowers product development costs.
- Uses new features and functionalities that reduce downtime and total cost of ownership.
- Customizes workflows, data models, and user interfaces, providing a flexible, traceable, and interoperable system that responds quickly to market, customer, and regulatory changes.
5. Autodesk PLM 360
https://www.autodesk.com/autodesk-university/class/Autodesk-PLM-360-Beyond-Traditional-PLM-2013
The PLM 360 software is a cloud-based tool that benefits all parts of an organization. It has pre-configured applications that enable various functions.
Key features and functionalities
- The quality management app provides a clear perspective of the decisions that influence the quality and cost of a product.
- The procurement apps help choose and assess suppliers and predict material needs.
- Asset management apps help to collect and assess data.
6. PTC Windchill
https://www.ptc.com/en/products/windchill
The PTC Windchill product lifecycle management software uses standardized and innovative functionality that helps businesses realize value faster. It provides simple and secure data access across the various teams in a business and enables a data-driven manufacturing approach.
Key features and functionalities
- Helps to manage data at scale using web architecture created for managing multiple systems.
- Uses IP and platform-based protections that provide a protected work environment inside and outside of an organization.
- Minimizes user disruption by using time-saving automation to upgrade data in real-time
- Leverage IoT-based continuous monitoring for enhanced service and support.
- It offers collaborative product development and product data management.
- Streamlines business operations by unifying partners, manufacturers, and supplies using real-time data sharing, integrated workflows, and change control for quick, secure, and efficient PLM.
Case Studies and Best Practices
When used effectively, agile PLM applications can connect and organize information, technology, and business processes, enabling faster time to market. Here are some examples of how companies have used these technologies to gain a competitive edge.
Application of PLM in Industry 4.0 environment
Case Study #1
Siemens has been instrumental in reducing the time-to-market and production costs for Electrolux via its Teamcenter PLM tool for Electrolux. The Sweden-based Electrolux AB sells commercial and household appliances used worldwide in over 150 countries.
Implementing Teamcenter in their manufacturing has saved over $2 million in buffer space and related investments, safeguarded plant designs, and optimized new plants without delays or errors.
Case Study #2
Aras Innovator helped Drager, a global manufacturer of medical and security technology, build secure systems. Drager used Aras Innovator for its digital transformation, enabling enhanced security, better scalability, cost savings, and high performance.
Case Study #3
To counter the mounting challenges brought on by product complexity and competition, Volvo used PTC Windchill for its growth and transformation. The PLM solutions incorporated by PTC Windchill helped improve sustainability and efficiency across Volvo's global operations.
It helped in expanding product offerings and reduced overall costs and time taken. A significant enhancement in quality elevates the customer experience. Manufacturing efficiency improved by consolidation of production processes. A shorter design cycle and reduced material waste resulted in cost reduction and sustainability.
Lessons learned and best practices for adopting PLM in the context of Industry 4.0
The advantages of PLM integrated with Industry 4.0 are numerous. However, the integration can fail to deliver the desired outcomes for many reasons. For instance, the lack of clear objectives or the inability to measure success can be a drawback. Improper guidance and a lack of vision can also be a hurdle. Here are some best practices that can help adopt PLM in an Industry 4.0 environment.
- Product lifecycle management software can be used as a platform for AI adoption, where data can be stored, managed, and analyzed. It can also help access and apply AI tools across various stages of a product's lifecycle, like testing, optimization, ideation, and simulation.
- It can facilitate IoT adoption by enabling integration, management, and security of data flows across the cloud, user, and product. It can help collaborate and coordinate between stakeholders and systems involved in developing, deploying, and maintaining the product.
- The design process can be revolutionized by using AR (Augmented Reality) and VR (Virtual reality) technologies. They can help in effective simulations of product models, which help monitor and assess every minute aspect.
- PLM can help in the adoption of digital transformation by providing a platform to streamline and coordinate product lifecycle processes. Industry 4.0 technologies like AR, VR, IoT, and AI can be integrated efficiently with other systems like Enterprise resource planning (ERP), Manufacturing Execution Systems (MES), and Customer Relationship Management (CRM).
Challenges and Considerations
While technological advancements have exploded, not all industries know how to implement them effectively. Some of the challenges that firms face in adoption of PLM include:
1. The cost factor
Many organizations find the initial cost of purchasing PLM software, its implementation, and training prohibitive.
How to overcome:
Conducting a cost-benefit analysis will help determine the long-term return on investment. Cloud-based solutions have more flexible costs. Choosing scalable solutions helps with phased implementation.
2. Security and Compliance
Organizations can find it difficult to ensure the agile product lifecycle management software system conforms to the prevailing industry regulations and secures sensitive data.
How to overcome
While using the system, a firm should ensure that it complies with the relevant regulations and standards. Strong security measures such as access controls and encryption and regular software updates can protect against vulnerabilities.
3. Skill gaps
Organizations find it difficult to ensure users of the software are adequately skilled.
How to overcome
Create a comprehensive program to train users for the various roles and continue providing resources and support. Making iterative changes based on user feedback can also help.
4. Resistance to adoption
Fear of using new technology or finding comfort in existing systems can prevent employees from adopting new processes.
How to overcome
Implementing an effective organizational change management approach that spans policies, work culture, technology, work routine, and procedures is needed. Communicating the advantages to all stakeholders, providing a learning and adoption plan, and supporting the change can help.
The importance of a holistic approach to PLM implementation
Implementing PLM successfully needs a holistic approach that involves initiating changes across various spectrums, such as:
- A properly documented and well-communicated product development approach.
- Aligning and coordinating across various business process domains.
- The use of strong and mature program management processes.
- Manage technical resources in relation to overall deployment.
Conclusion
PLM and Industry 4.0 integration has paved the way for accelerated end-to-end processes. The use of Industry 4.0 technologies drives agile product development and fosters a well-coordinated and connected value chain that includes suppliers, manufacturers, and customers. This article sheds light on what are PLM tools, their integration with innovative technologies, and the resultant benefits, challenges, and ways to overcome them.
For successful outcomes, it is necessary to continuously adapt to changing trends and nurture innovative processes. Regular review and upgrade of the existing systems that allow for leveraging new capabilities and functionalities is the need of the hour. This will help organizations realize all the benefits of their investment.