The Role of Advanced Software in Modern Manufacturing
Steam engines, factories, and textile machinery set the ball rolling for the First Industrial Revolution in the 1700s. Subsequent advances in manufacturing gave way to the Second, Third, and Fourth Revolutions. The main factor behind the various revolutions was the need to speed up manufacturing without much human input.
We are now in the fourth revolution, which is called Industry 4.0. In this latest phase, software plays a significant role. Software helps improve efficiency and accuracy and makes organizations competitive. This has led to an increased demand for manufacturing software development.
Up until 2022, around 816 million people were employed in industries globally. Companies need the right tools to create business value and compete in a tough market situation. This is where advanced software and its benefits for manufacturing gain significance. Nearly 88% of small business owners state that automation helps them compete with large firms, and 78% of executives state that AI applications can create business value.
The use of software for manufacturing companies is expected to reach $355 billion by 2030, with a CAGR of 13.5%. Besides the core industrial value chain, software used in the manufacturing industry also deals in cloud services, cybersecurity, and more. Businesses can use the right software companies to ensure better performance and higher ROI. This guide gives a deeper insight into the role played by advanced software in manufacturing.
The Importance of Software in Modern Manufacturing
Manual processes are prone to errors and can be expensive to industries in terms of time, effort, and money. The software enhances operational efficiency, making businesses more productive and competitive. The usage of software in manufacturing is predicted to grow at a CAGR of 5.4% from 2023 to 2030. Software used in the manufacturing industry can make better and quicker decision-making, a safer workplace, superior product quality, and real-time monitoring possible.
Examples include ERP (Enterprise Resource Planning) software, which is an invaluable addition to production planning and improvement. MES (Manufacturing Execution Systems) is another important software in manufacturing. It monitors, documents, and controls the business processes from raw material sourcing to finished products.
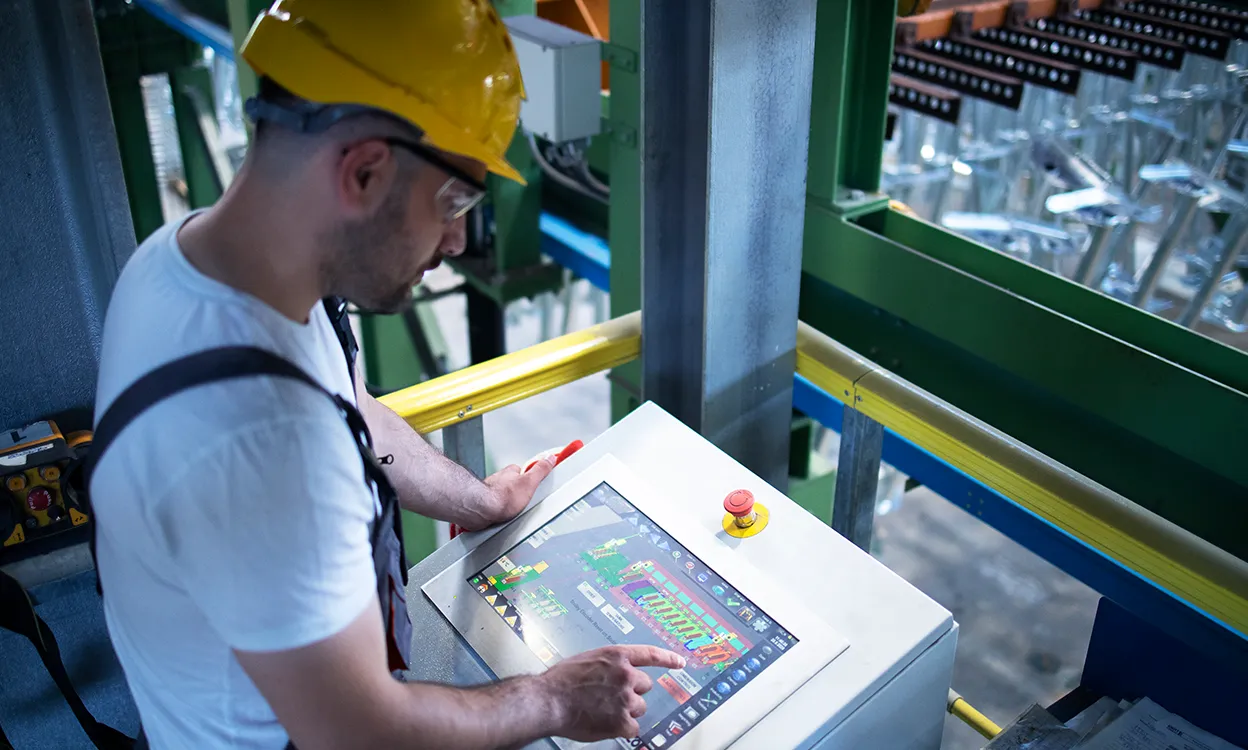
Key Types of Manufacturing Software
The primary purpose of using software in manufacturing is to save time and minimize waste. Therefore, the type of software used varies based on the application and functionality.
ERP Systems
Enterprise Resource Planning software ensures multiple business processes are controlled under a single managing system. Some of the main functions of an ERP include:
- Managing inventory
- Project management
- Managing supply chain processes
- Procurement
- Risk management and compliance
- Financial management
Here are the top 6 manufacturing ERP systems that stand out in 2025:
- SAP S/4HANA: SAP's flagship ERP solution offers comprehensive functionality for manufacturers of all sizes. It provides real-time insights into manufacturing processes, enables quick adjustments to demand changes, and supports better decision-making. SAP S/4HANA is particularly suitable for large enterprises and complex manufacturing operations.
- Oracle NetSuite ERP: This cloud-based solution is popular among manufacturers, especially in process industries. NetSuite ERP offers integrated functionality across large enterprises, including supply chain management, production planning, financial management, and real-time analytics. It's known for its scalability and ability to handle global operations.
- Microsoft Dynamics 365: This ERP system provides a comprehensive suite of tools for manufacturers, including production planning, inventory management, and financial integration. It offers strong integration with other Microsoft products and focuses on data analysis and reporting. Dynamics 365 also includes IoT integration for real-time monitoring of production processes.
- Epicor Kinetic: Formerly known as Epicor ERP, this solution is designed for manufacturing and distribution industries. It offers a full range of supply chain management capabilities and industry-specific solutions like Advanced Planning and Scheduling (APS), Manufacturing Execution System (MES), and Configure Price Quote (CPQ).
- Infor CloudSuite Industrial: Previously known as SyteLine, this ERP system is well-suited for discrete manufacturers. It offers robust capabilities for complex mixed-mode manufacturing and is particularly strong in areas like shop floor control, quality management, and detailed product costing.
- Acumatica Manufacturing Edition: This cloud-based ERP is an excellent choice for small to mid-sized manufacturers. It provides a comprehensive suite of connected business applications, including production management, estimating, engineering, material planning, scheduling, and product configuration. Acumatica is known for its flexibility and user-friendly design.
These ERP systems offer a range of features essential for manufacturing operations, including inventory management, project management, supply chain processes, procurement, risk management and compliance, and financial management. By implementing one of these top ERP solutions, manufacturers can enhance their operational efficiency, improve decision-making, and stay competitive in an ever-changing market landscape.
MES (Manufacturing Execution Systems)
MES software for manufacturing companies helps in the entire process of production of goods, from raw materials to end products. They monitor, track, document, and control processes. It acts as a bridge between process control and ERP systems. This results in better efficiency and optimized production. Industries that use this type of software include
- Defense and biotechnology
- Food and beverage
- Pharmaceuticals
- Aeronautics and aerospace
- Medical devices
This software, used in the manufacturing industry, can ensure products adhere to compliance and regulations. The MES market size, which was 14.9 billion USD in 2024, is predicted to reach 23 billion by 2029.
CAD and CAM Software
CAD (Computer-Aided Design) and CAM (Computer-Aided Manufacturing) software tools automate manufacturing.
They are used in machinery, milling, laser cutters, and printers. They help to accelerate repetitive tasks and ensure accuracy. Manufacturers can directly create goods from a computer design.
Mechanical, electrical, and aerospace engineering find the CAM helpful software. Air-conditioning and refrigerator manufacturing also benefit. CAD is applicable in industries like:
- Aerospace and aviation
- Civil and structural manufacturing
- Consumer products
- Medical devices
- Oil and gas industries
Quality Management Systems (QMS)
Meeting regulatory and customer requirements is key to business success. QMS can achieve this by documenting processes and procedures. It helps to achieve quality objectives and policies. Software in manufacturing gives the advantage of automation. Quality processes are managed in a streamlined way. Benefits of QMS include
- Automated workflows
- Enhanced data integrity
- Improved accessibility
- Support compliance
Document control, change control, training management, compliance management, and supplier management are some of the primary uses of QMS software in manufacturing.
Predictive Maintenance Tools
PdM (Predictive Maintenance) tools are useful to organizations as they help in improving equipment reliability. They can monitor conditions to ensure optimal results. Some of the key PdM tools in use are:
- Ultrasonic analysis
- Vibration analysis
- Motor circuit analysis
- Laser-shaft alignment
- Infrared analysis
- Oil analysis
In recent times, PdM has used IoT to collect real-time data. The information is used to predict equipment failures. It helps in timely intervention, which reduces downtime. Maintenance schedules are optimized, resulting in huge cost savings. PdM can reduce maintenance costs by 10% and improve equipment uptime by up to 20%. The monitored metrics, such as pressure, temperature, etc., are analyzed using AI to spot failure patterns. AI helps predict future performance, resulting in proactive and informed decision-making.
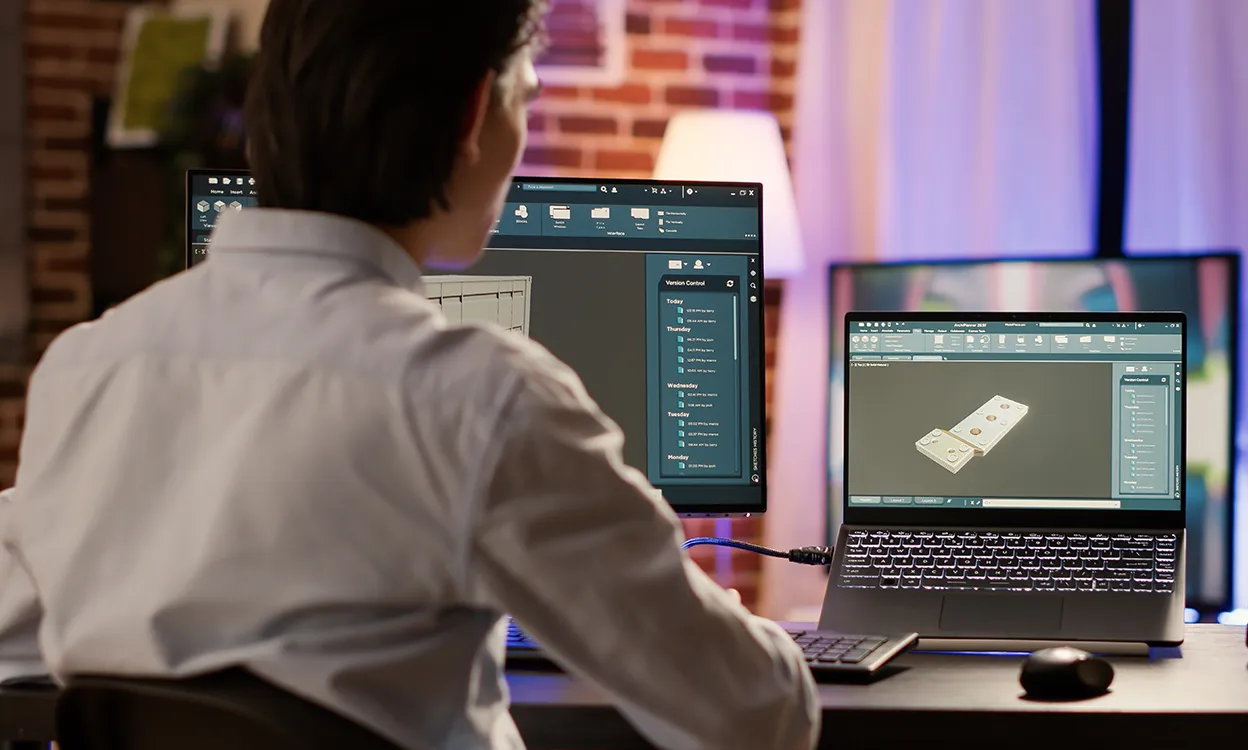
Emerging Trends in Manufacturing Software
The constant advancements in software technology have brought a marked shift in manufacturing. From designing to delivering products, technology is revolutionizing the industry. Here are some of the key emerging trends in the use of software in manufacturing.
Industry 4.0 Integration
The fourth industrial revolution characterizes a blend of biological, physical, and digital systems. It uses IoT, robotics, and AI technologies to improve business ecosystems. Reduced cost, greater customization, and improved efficiency are possible. Real-time monitoring is enabled, and decision-making is enhanced.
One of Industry 4.0's benefits is the application of 5G. 5G connectivity can improve network reliability, device communication speed, and system flexibility. It helps in automation, improves remote equipment control, and ensures resilient operations.
Smart factories concept that integrates robotics, AI, and IoT helps in advanced automation. Streamlined maintenance, automated responses, and enhanced asset performance are possible. A 2023 survey reveals that 97% of respondents intend to use smart manufacturing technologies. Manufacturers support the smart factory concept as it can
- Minimize costs
- Accelerate production based on changing demand
- Minimize reliance on manual tasks
- Reduce product defects
- Improve process efficiency
Cloud-Based Solutions
A cloud-based software used in the manufacturing industry is key to data management and analysis. Cloud infrastructures work by collecting, storing, and processing data. They analyze collected information to help make equipment reliable and operations more optimized.
Insights are unlocked in real-time, which encourages effective and responsive operations strategies. Reduced costs and downtime are some of the benefits.
Firms using such solutions can scale up or down based on their needs without investing more capital. Remote access is easier via a wide range of mobile devices. Data sharing is easier. Further, the service provider takes care of data security and software updates. This avoids spending on paid professionals to fix IT issues.
AI and Machine Learning Applications
Using AI and ML in manufacturing helps meet production demands and changing market conditions. Machine learning provides accurate demand predictions, which optimize inventory and prevent over- or under-stocking.
Artificial intelligence enables streamlined supplier selection and management. It identifies reliable suppliers by analyzing cost, reliability, and quality. AI also identifies ideal delivery routes, resulting in efficient logistics and product distribution. AI and ML can help control warehouse systems, ensuring effective layout and storage.
Other areas where the technologies can be beneficial include predictive maintenance and production planning. ML helps in precise and speedy inspections, resulting in early detection of defects, which helps in timely resolution. ML also predicts potential failures, enabling minimal downtime.
Blockchain for Supply Chain Transparency
Blockchain is useful not only in the digital currency sector but also in the digital currency sector. It can be highly beneficial in managing supply chains. The software in manufacturing can provide advantages such as
- Faster and cost-efficient product delivery
- Improved traceability of products
- Better coordination between stakeholders
- Help in financial access
Blockchain technology assigns unique identifiers to inventory, loans, orders, and bills. All aspects of a transaction are recorded and encrypted. Every person involved in the supply chain process will have individual copies of the transaction. This makes it easier to identify errors and ensure they are resolved, ensuring trustworthy and failproof supply chain management.
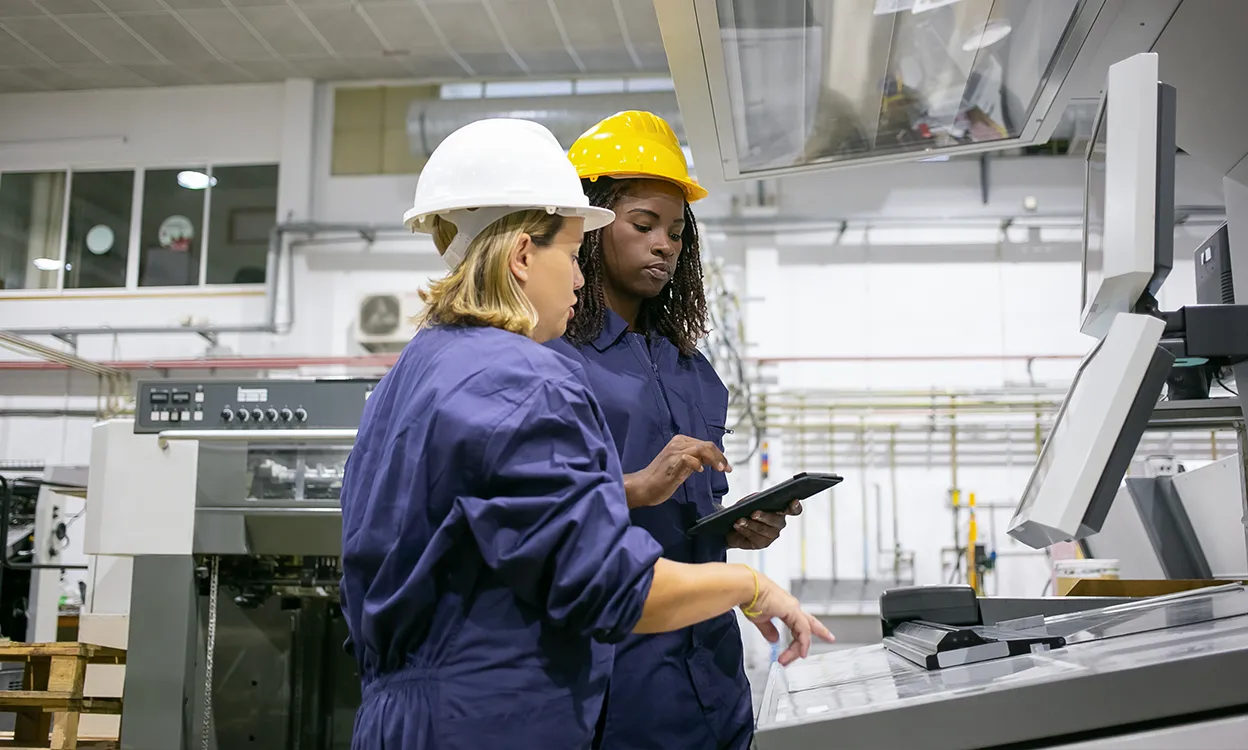
Benefits of Advanced Software for Manufacturing Companies
To overcome the challenges faced in the highly competitive manufacturing sector, companies need advanced software in manufacturing. The use of software in manufacturing has brought a marked shift in the operations of many organizations. Some of the key benefits of software used in the manufacturing industry are:
Efficient processes and productivity boost
The main advantage is the impact on the bottom line. Better productivity and efficiency are assured with the use of advanced software. The use of automated systems and analysis of data in real-time ensures
- Reduced downtime
- Smooth operations
- Optimized use of resources
For example, Walmart uses artificial intelligence to manage its supply chain. This enhances productivity and ensures customer satisfaction. ML is used to predict customer demand, assess sales data, and manage the inventory. Guaranteed availability of products and avoiding stockout situations are possible with the advanced applications.
Enhanced flexibility to adjust to market dynamics
Given the ever-changing market dynamics, companies need to be able to adjust to changing conditions quickly. By using software in manufacturing, companies can gain the flexibility required to encounter changes, such as
- Altered production schedules
- Disruptions in the supply chain
- Changing customer demands
Giving organizations this type of flexibility can shorten product life cycles. It also enables them to customize their products to the maximum.
Example: NVIDIA uses advanced technologies like AI and ML to predict market changes. It uses software in manufacturing to examine huge datasets. Possible issues in chip designs are identified and rectified. Reduced expenses, better yields, and optimized layouts are enabled. The time to market is also quicker with AI and ML software used in the manufacturing industry.
General Electric also uses AI to analyze data from historical records and sensors to identify buying trends. The software used in the manufacturing industry can predict equipment issues and help in process streamlining. Software in manufacturing assures improved equipment effectiveness, reduced downtime, and enhanced efficiency.
Optimizing resources and cutting down waste generation for better sustainability
Software used in the manufacturing industry can help organizations achieve their sustainability goals. According to the International Energy Agency (IEA), data centers use nearly 1% to 1.5% of global electricity. Consumption can be reduced by using efficiency-enhancing and waste-minimizing tools. ERP software, which is used to manage finances, inventory, and supply chains, can enable this. Companies can reduce waste by optimizing their processes using this software.
Example: Starbucks uses Oracle ERP. This ERP tool is a cloud-based system that helps to automate daily operations and back-office systems. Other benefits of the tool include
- Manage projects, finances, and supply chain.
- Take care of procurement and accounting.
- Manage human capital and customer relationship
- Handle analytics, business intelligence, and more.
With its various functions, the ERP tool ensures optimized processes. This helps reduce waste and save on costs. Businesses can assess the environmental impact and improve their sustainability efforts. By minimizing waste, limiting environmental effects, and increasing efficiency, the company's long-term viability is enhanced.
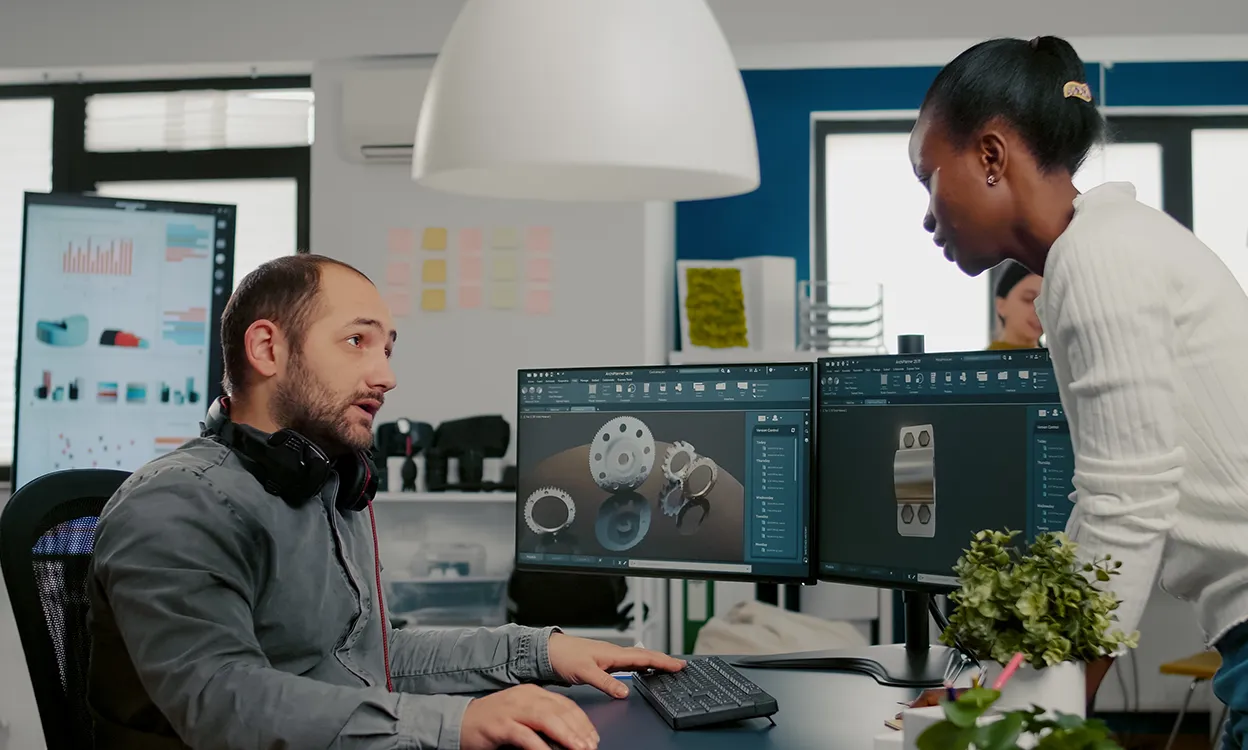
Challenges in Implementing Manufacturing Software
While industries can reap many benefits from using software, they also face some challenges. Here, we discuss the main challenges that industries face in adopting software in manufacturing and how to address them.
Initial costs
The cost of implementing the software is a major challenge, particularly for small and medium businesses.
When businesses view the initial set-up costs as a long-term investment, they will not be a big burden. Some services offer a pay-as-you-go model, where a business pays only for the functions required. As the business grows, it can opt for additional functionalities.
Integration difficulties
Adding advanced software to existing technology can be problematic. Compatibility problems may arise, making it difficult to use the software effectively.
Conducting a preliminary audit of the IT systems and shortlisting stages will ensure seamless integration.
Training employees
Employees require time and guidance to adapt to the software used in the manufacturing industry. Insufficient training can sabotage the technology's benefits.
Resistance and training issues can be solved by providing training and ongoing employee support. Another way is to choose an application that is simple and user-friendly.
Security issues
While the use of advanced software for manufacturing companies is beneficial, protecting business and employee information is also a concern. This is particularly important when using cloud-based systems.
To overcome security concerns, businesses must choose packages with built-in data protection and strong encryption. For cloud-based software, using suppliers offering accreditations like ISO 27001 can help. Choosing service providers providing backup, disaster recovery, and security features will also ensure robust security.
Scalability
Choosing software for manufacturing companies that can adapt to the changing needs of a business is a vital criterion.
Ensuring the service provider offers scalable software will ensure no scalability issues. Using software customized to the business's needs will ensure seamless functionality.
Maintenance
Update the software regularly to ensure smooth performance and security. This can pose a challenge in the long term.
Instead of making it a tedious process, updates should be seen as opportunities to improve the software's efficiency. Maintenance and updates can be avoided when using cloud-based systems, which can be a major deciding factor when choosing the solution a business needs.
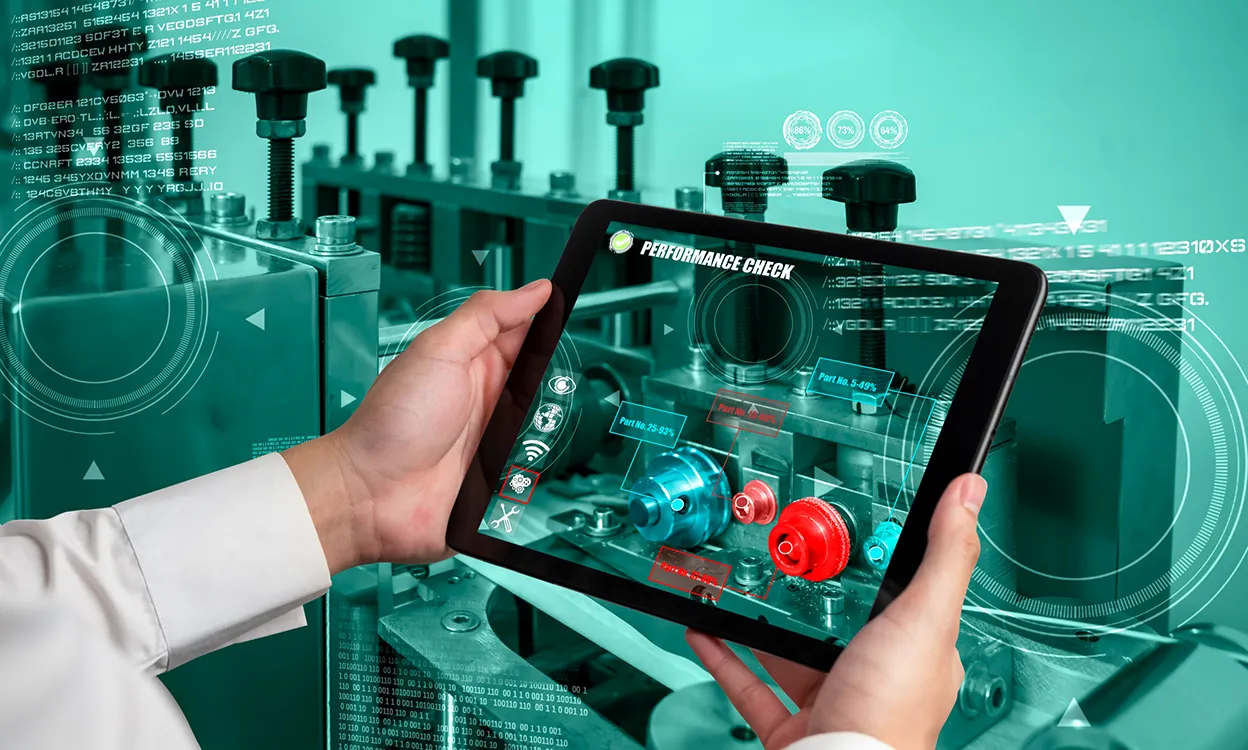
The Future of Manufacturing with Advanced Software
Changing market dynamics in the manufacturing sector necessitates using advanced software to meet competitive challenges. The huge gap in finding skilled labor has affected industries like manufacturing, healthcare, construction, and others. Using advanced software tools can address the gap and ensure productivity. Some of the future trends in software used in the manufacturing industry are discussed below:
Deeper AI integration
As manufacturing adapts to market and technology changes, the integration of AI has become more pronounced. Some of the advancements in leverage AI include
Deep learning methods will be used increasingly to optimize manufacturing processes. Neural networks and deep learning methodologies make sophisticated decisions easier.
Edge computing will dominate as it helps process data in real-time. Source-level decision-making will improve scalability, minimize latency, and boost system reliability.
Complex AI systems, such as explainable AI models, will be used. This will help increase transparency and facilitate understanding of the manufacturing processes.
Digital Twin simulation
Digital twins are virtual replicas of production lines, supply chains, and factories. The replicas are used to simulate, assess, and predict real-time performance. This technology allows better monitoring and optimization of operations.
Digital twin technology uses the Internet of Things (IoT), deep learning, AI, and Programmable Logic Controllers (PLCs). These help update the digital twin model with live information, ensuring an accurate and updated virtual replica.
Personalized manufacturing
Using technologies like AI ensures products are customized according to individual preferences without impacting production. Integrating AI in the design process can help adapt designs based on consumer feedback.
Besides the above trends, there are many others, such as augmented reality, virtual reality, and robotics. With Industrial IoT, these can act as connected solutions to monitor, analyze, and improve performance. Continuous innovation in manufacturing software development will be a driving force for the industry's growth and development in the future.
Conclusion
Introducing advanced software for manufacturing companies can be transformative. By integrating such technologies, manufacturing can become data-driven and automated. Smart factories with self-optimized machines may become a staple in the field.
As technologies like IoT become more prevalent, supply chain efficiency will be enhanced. Greater customization and sustainable manufacturing can become a reality.
Manufacturing software development can contribute immensely to adopting greener operations. Reduced waste and optimal resource use will enable this transformation. With constantly evolving technologies, the future of manufacturing holds great potential.
Manufacturers need to realize the immense potential of using such innovative software. Besides making operations more straightforward and more accurate, they can help manufacturers compete and flourish in the constantly changing marketplace.